Inventory management is a concept and technique used to organize and optimize a company’s or business’s stock of goods or products. In this article, we’ll discuss what it is, its purpose, and the most commonly used inventory management methods.
What Is Inventory Management?
Inventory management is the process of controlling and overseeing the stock of goods owned by a business or company.
This inventory may consist of finished products, raw materials, or work-in-progress items still in the production process.
The purpose of inventory management or stock management is to ensure that the right amount of stock is always available to meet customer demand—while minimizing holding costs and potential business losses.
In fact, inventory management is one of the most critical aspects of business operations, especially in the F&B industry.
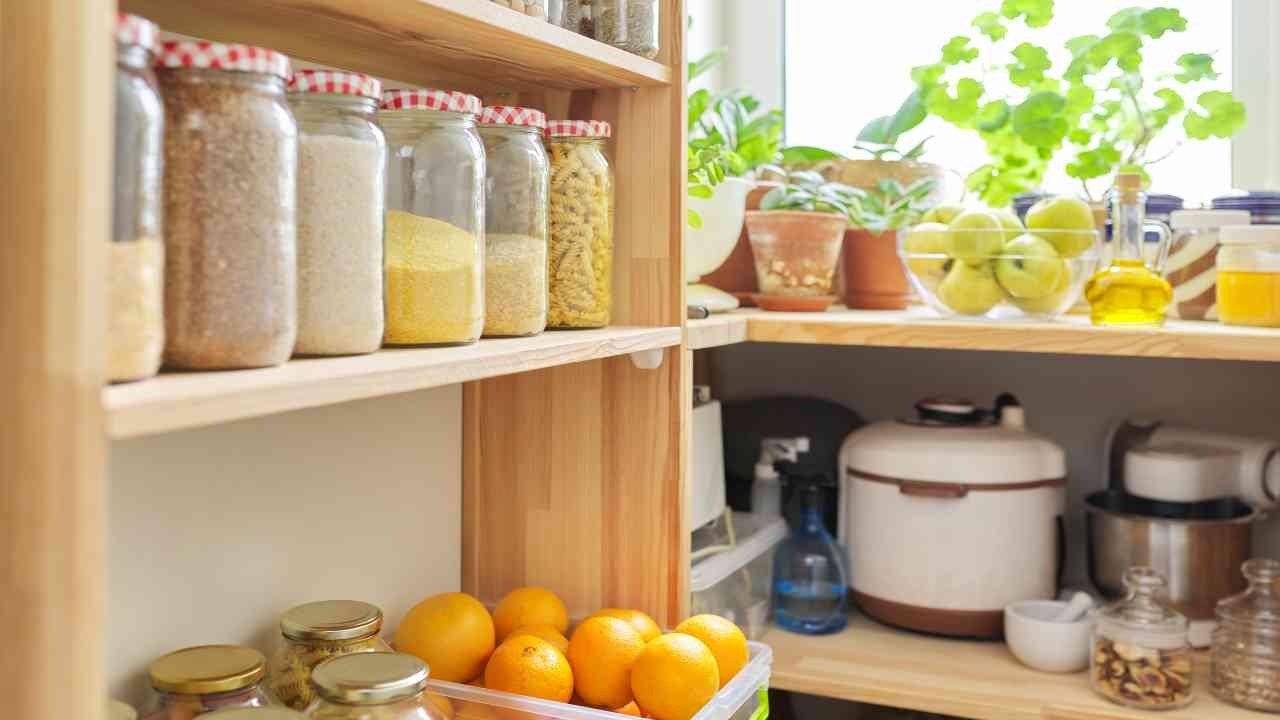
Objectives of Inventory Management
The primary goal of inventory management is to ensure that stock levels are always sufficient to meet customer demand. This directly supports customer satisfaction and helps boost profitability.
Customer satisfaction plays a major role in a company’s brand and reputation. In the long run, businesses that maintain high customer satisfaction usually have a stronger potential for long-term success.
Inventory management also aims to minimize inventory-related costs, such as storage fees and inefficiencies in production. Reducing these costs helps businesses save money and operate more efficiently.
Read: How to Manage Stock Effectively to Avoid Business Losses
Inventory Management Methods
There are several methods commonly used in inventory management. Here are some of the most popular ones:
First-In, First-Out (FIFO)
FIFO is an inventory method that prioritizes the oldest items in stock to be sold or used first.
This ensures that older inventory is cleared before newer items, reducing the chance of products becoming outdated or expired.
Last-In, First-Out (LIFO)
LIFO is the opposite of FIFO—where the most recently acquired stock is sold or used first. This method is commonly used in industries like agriculture or livestock, where raw materials may need to be rotated differently.
Minimum Stock Level
This method ensures that a business always maintains a minimum inventory level to meet customer demand.
It allows companies to forecast needs and avoid running out of stock, ensuring continuity in operations.
Just-In-Time (JIT)
The JIT method means stock is ordered only when needed—avoiding the storage of unsold goods.
It reduces excess stock and minimizes storage costs, improving efficiency across operations.
ABC Analysis
ABC analysis is a method of classifying inventory based on importance and customer demand.
Products with high value and demand fall into category A, while less critical items are categorized as B or C.
In conclusion, effective inventory management helps businesses prevent loss and maximize profit.
However, manually managing inventory can be time-consuming and difficult. That’s where Opaper comes in to simplify the process.
Opaper is an online inventory management platform designed to help businesses organize their stock more efficiently.
With Opaper, you can monitor inventory in real time, forecast demand, manage orders and payments, and even track product deliveries.
It also provides complete and detailed analytics, helping you make better decisions based on accurate data—minimizing risks and boosting profitability.
Plus, Opaper is easy to use and accessible anytime, anywhere—whether from desktop or mobile. You can manage your stock on the go.
So, what are you waiting for? Download Opaper today and take your inventory management to the next level. With Opaper, managing your inventory becomes easier, more efficient, and more profitable.